Tight Done Right
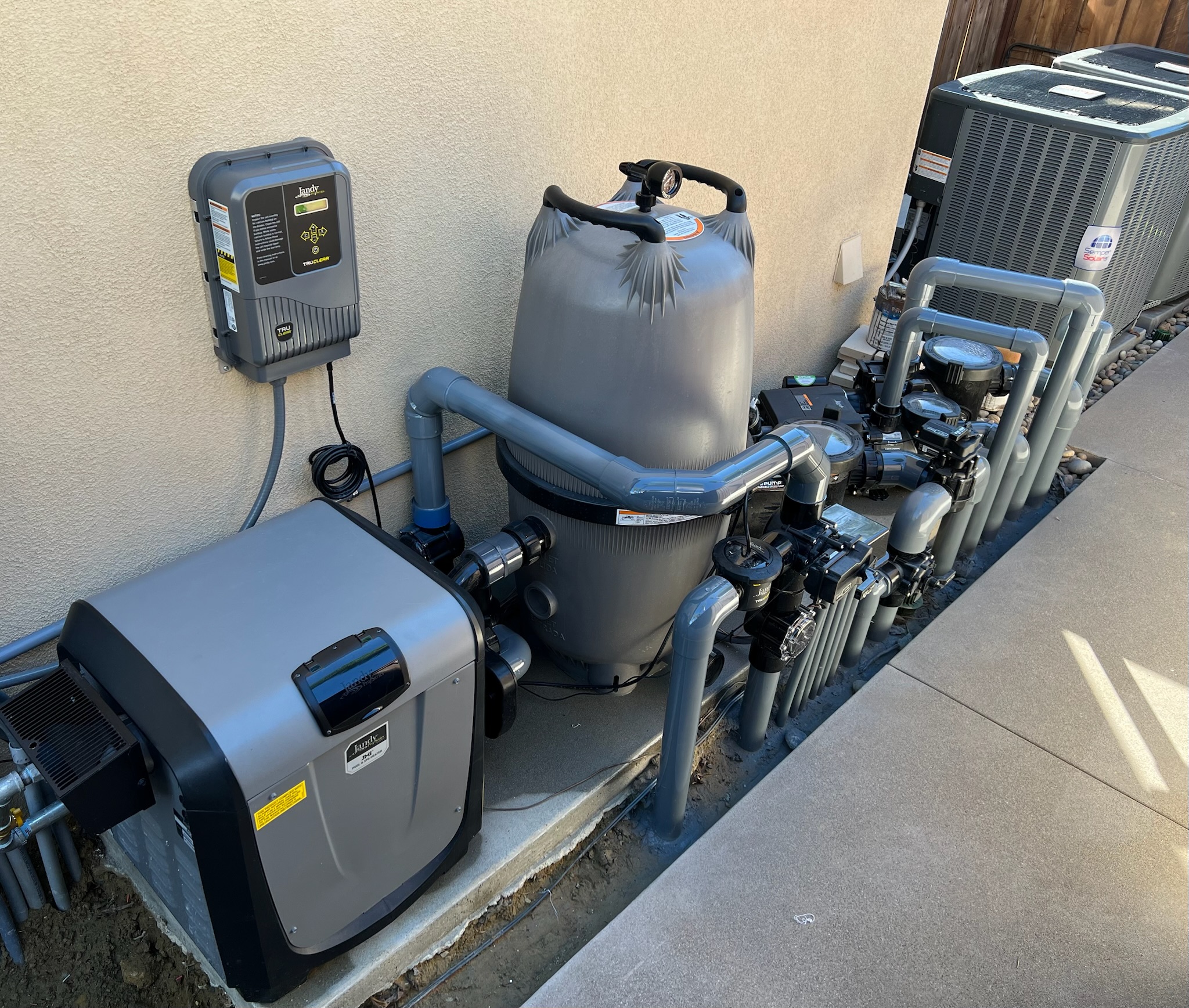
Customers are often eager to complete their backyard oasis with a pool, but limited space, system demands and aesthetics can compete with utilities, setback codes and property lines. With proper planning, pool pros can optimize small equipment pads without sacrificing performance, maintenance or visual appeal.
Client needs drive the process
The true foundation of equipment layout is understanding a client’s vision, which dictates the size and complexity of equipment needed. Even small pools may require multiple pumps, larger heaters and bigger filters when a client wants year-round usage or premium features like swim jets and automatic covers.
Also consider future plans beyond the current project. Decks, pool houses, accessory units and solar utility systems can impact space and serviceability. Clients may get inspired to make changes later, but at least you’re asking the right questions upfront.
Serviceability and preventative maintenance
Space-saving equipment layouts should never sacrifice serviceability. Allow enough space for different technicians — big or small — to quickly access components, with enough clearance to easily remove filter lids, filter cartridges and pump baskets.
“I’ve come back to pools where clients chose to add a deck,” says Connor Gibbs, vice president of Gib-San Pools in Toronto. “It wasn’t directly on top of our equipment, but it didn’t allow for enough clearance to remove a filter cartridge,” he says. In collaborating with other contractors, Gibbs says, “The key is keeping that open line of conversation and understanding that we’re not competing. We’re working together to achieve the client’s end goal.”
Preventive maintenance is also important. Overgrown plants can obstruct access to equipment, and dust and debris can compromise functionality.
“Our service team is not there to just clean the pool,” Gibbs says. “They’re moving leaves out of the equipment area, washing down the pad and making sure empty containers are removed. That platinum level of service shows you really care, and it doesn’t take that much more time.”
Optimizing tight spaces
Early in the process, before breaking ground, plan the equipment pad to understand its placement and fit. Separating or stacking equipment is a great strategy to optimize space as long as components are grouped for serviceability.
“If you have the pump or filter very far from the pool panel, it will be inconvenient to service,” Gibbs says. “Typically, you want things that need to be serviced concurrently in the same location.” For example, grouping the pump and in-floor cleaning headgear system in one location and the heater and filter in another.
Typically, you want things that need to be serviced concurrently in the same location.”
Connor Gibbs, Gib-San Pools
When stacking equipment, Brennan Warde of ARC Pools in San Diego is partial to Jandy residential products because of its compact design.
“The vent is easy to change if we need a stack vent, and the vent grill doesn’t get very hot,” he says. “I’ve put those heaters in some pretty interesting spots, and they do really well.” Warde puts the heater on a table, with pumps underneath and the filter standing beside it.
Using Jandy pumps, heaters and filters, Warde has tucked equipment under stairwells with only 3 feet of vertical clearance. “Everybody was shocked,” he says. “But you can work on it because you can still get to it from both sides.” Attention to detail is a design philosophy Gib-San Pools and ARC Pools champion, ensuring equipment and piping are organized to look clean and professional.
Regional considerations
In sunny San Diego, pool builders must consider intense heat, heavy rain and earthquakes. Poured concrete pads are still common, but the team at ARC Pools also likes prefabricated equipment pads — basically, a plastic foam panel sprayed with a cementlike mixture, creating a lightweight and movable pad.
“We put them on a bed of compacted dirt and gravel for drainage,” Warde says. “If you ever have to fix plumbing or change something, those pads can be lifted off for easier access.”
However, Warde notes that when equipment is stacked on a table, a concrete pad is needed to bolt it down.
In frigid Toronto, pool builders must consider freeze-thaw cycles and cold weather usage. Increasingly, 365-day pools are popular, and a natural gas heater is the standard. Combined with small yards and laneway garages, serviceable equipment layouts are challenging.
“Natural gas-integrated generators need an insulated and heated space,” Gibbs says. “To avoid scaling issues, you might also consider a boiler and heat exchanger. That can be easier and doesn’t have the same failure points as a natural gas pool heater.” Either way, it’s common for equipment to be installed in the corner of the client’s garage.
Thoughtful renovation
Space can be a challenge when renovating older pools. The Gib-San team pays close attention to water hydraulics and the potential for increased efficiency. They also enhance the pool’s performance by using new and current materials, which improve aesthetics and reduce damage from freeze-thaw cycles.
“[In Toronto], our pools typically all run 24/7,” he says. “In some cases, a pump fails and turns off. Where does that water go? Planning for ‘what-ifs’ is important for the longevity of that equipment.”
Even the tightest spaces are an opportunity to deliver exceptional results. With careful planning and service-focused design, pool pros can create efficient, serviceable installations.